Surface Mount Soldering
Surface mount soldering is the process of creating circuits using surface mount technology (SMT) components that are mounted directly onto the surface of printed circuit boards (PCBs).
SMT technology is a key driver in the ever-important work of miniaturization of circuits, allowing for smaller, lighter devices with ever-increasing capabilities.
Today’s cell phones have exponentially more computing power than the massive supercomputers that controlled the Apollo space missions. The manufacture of PCB circuits via surface mount soldering was a key breakthrough that makes this possible.
Process
A pre-printed PCB outlining the circuit, with solder pads indicating component locations and connections, is matched with a stencil that directs the application of solder paste.
Solder paste is a gelatinous mixture of powdered conductive metal (commonly tin) and flux, which is a liquid or semi-liquid chemical compound that acts as a binding, cleaning, and wetting agent.
The solder paste is commonly spread in a wide swatch over the stencil, which directs it to only those solder pads where components are to be attached and allows for easy reclamation of excess paste for re-use.
Once the paste is applied, a conveyor belt runs the PCB through a pick-and-place machine where components are simply set onto the board. Tolerances for placement are generally relatively more forgiving than other solder methods, as the coming reflow process will automatically align the components on their pads.
When both paste and components are in place, the PCB then transits through a reflow oven, which heats the board at a rate designed to melt the solder paste without damaging the components. The reflow process liquefies the metal component of the solder paste, cementing the contact points of the electrical components to the PCB and ensuring electrical conductivity, while common evaporating the excess flux. The surface tension of the molten solder helps keep the components in place.
Reflow ovens for surface mount soldering typically come in one of three categories: convection, infrared, or vapor phase
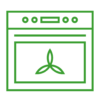
Convection
Convection is the most common as it allows for equal heating of the entire board, which prevents the issue of some solder paste locations not reaching the melting point. This equal heating, though, requires tighter overall control as PCB components are subject to the same heat and can be damaged by it.
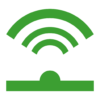
Infrared
Infrared allows for much more pinpointed heating to be applied, significantly reducing the risk to components, but drastically reduces tolerances for misalignment and resultant failure of the solder paste to melt and form the necessary bond.
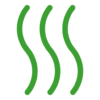
Vapor
Vapor phase removes both risks, but requires expensive, specialized equipment to handle the fluorocarbon liquids with high boiling points and mitigate the environmental risks associated with those compounds.
Following reflow, a washing of the completed board is recommended. This both removes any stray solder balls that can cause short circuits, as well as remove flux residues that may have spread onto the PCB during the heating process.
Depending on the type of solder paste used, different solvents are required:
- No-clean fluxes are most common, and they do not require strict washing. The flux residue is considered harmless, and can simply be left on the board. However, a manufacturing process that skips the washing step requires a very clean assembly environment and may need an inert reflow environment to prevent conductive particles from landing on the board. If a conformal coating is to be applied, washing is still recommended, as the flux residue could cause those coatings to adhere less effectively.
- Water-soluble fluxes can be removed with a directed water spray, typically including a detergent compound
- Rosin-based fluxes require specific chemical solvents, generally involving fluorocarbons
Advantages
Because surface mount soldering allows for machine-guided placement of components and printed stencil-guided application of solder, a much more tightly packed circuit board is possible. The advantages here are numerous, including:
- Smaller components (from one-quarter to one-tenth the size and weight)
- Higher component density
- More connections per component
- Lower radiated emissions (due to the smaller radiation loop area and inductance inherent to smaller components)
- Lower resistance and inductance at the connection
- Cheaper components (again, generally due to smaller components – from one-half to one-quarter the cost of equivalent through-hole parts)
- Final products that both take up less space and have less mass
Surface mount soldering has also proven to be the most efficient and cost-effective process for mass-production of printed circuit boards. Because the setup is almost entirely automated equipment, there is less time, setup and labor cost involved, as well as simpler and faster operation once the process is in place. On the high-end, some pick-and-place machines are capable of placing more than 2,000 components per minute.
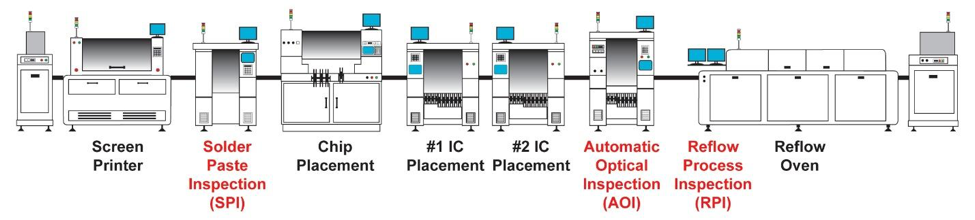
As mentioned previously, the reflow step key to the surface mount soldering process allows small errors in component placement to be corrected automatically as the surface tension of molten solder pulls components into alignment with solder pads.
Disadvantages
Because surface mount soldering relies on the surface tension of the melted solder paste to hold components to the board, it is not recommended for large components, nor those with high-voltage capacities. In PCBs that use transformers, heat-sinked power semiconductors, large capacitors, or fuses, either additional adhesive and/or a combination of both surface mount and through-hole soldering is used.
Through-hole soldering also adds a degree of mechanical connection between components and boards by extending leads through PCBs, contrasted to the simple seated SMT model. This means surface mount soldering creates a mechanically weaker connection and is not preferred for components that will be undergoing sheer force.
The key advantage of surface mount soldering, with the automation process allowing smaller and more dense packing of components, also means that repairs can be difficult.
Surface mount soldering is preferred over through-hole soldering because of the level of precision necessary to achieve that density, and that same density requires an extremely high level of precision, expertise, and often expensive equipment for repairs.
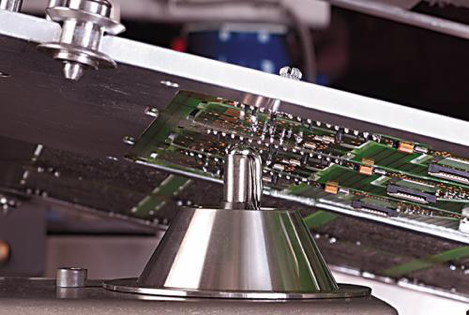
The higher speed and miniaturization in the production process can increase the risk of defects, so a failure detection process is recommended for any SMT manufacturing process. Surface mount soldering is prone to a variety of potential issues and these issues can begin with solder paste printing.
FCT Assembly and our partner BlueRing Stencils offer a variety of high-quality products which can improve the solder paste printing process.
Our solder pastes have excellent printability and long stencil life. Our stencils and nano-coatings are designed to improve the print process.
FCT Assembly offers technical support for the entire surface mount soldering process. Please contact us if you need help with surface mount soldering.