How Does Surface Finish Affect Solder Paste Performance?
There are many solderable surface finishes used on printed circuit boards. These surface finishes are necessary to protect the copper pads from oxidation and corrosion. Copper oxidizes very quickly and the oxide thickness grows over time. Copper oxides are very difficult to solder to especially with low activity no-clean fluxes. Solderable surface finishes protect the copper pads and holes while enabling good solderability.
Historically, the most common surface finish was tin-lead (Sn63/Pb37) hot air solder level (HASL). The process used to coat circuit boards with HASL is as follows. The copper is etched to remove oxides, then the circuit board is coated in hot air flux. The circuit board is immersed in molten solder. As the circuit board is removed from the solder hot air is used to “level” the solder making it relatively flat and clearing the holes.
Finally, the circuit boards are washed to remove flux residues. Tin-lead HASL has the inherent issue of being non-planar or “bumpy”. This can have detrimental effects on printing of solder paste and component placement.
Tin-lead HASL is still used today as it is also known to solder very well and is tolerant of multiple soldering cycles.
Lead-free HASL is a common finish that has replaced tin-lead HASL in many applications. The process used to coat circuit boards with lead-free HASL is essentially the same as the process for tin-lead HASL. The only exception is the solder alloy that is used. Tin-lead HASL uses Sn63/Pb37 alloy, while lead-free HASL uses tin/copper based alloys like SN100C. Lead-free HASL also has the inherent issue of non-planarity, but solders quite well through multiple soldering cycles. HASL finishes are very durable and hold up well to mechanical damage.
Organic solderability preservative (OSP) is a popular finish due to it’s low cost relative to the other surface finishes. The process used to coat circuit boards with OSP is as follows. The copper is cleaned and etched to remove contaminates and oxides. Then the copper is coated with an azole mixture. The excess liquid is removed and the coating is dried.
OSP must be handled carefully because it is susceptible to mechanical damage. OSP coated circuit boards must be protected from the air and moisture to prolong shelf life. OSP is flat so it does not have the same issues with non-planarity as HASL.
OSP is known to show issues with multiple soldering cycles and is mainly used for cost-sensitive applications that require a limited number of soldering cycles.
Electroless nickel immersion gold (ENIG) is a very popular surface finish. ENIG’s counterpart electroless nickel electroless palladium immersion gold (ENEPIG) is becoming more popular. The process used to coat circuit boards with ENIG is as follows. The copper is cleaned and etched to remove contaminates and oxides. Then the copper is coated with a metallic catalyst, like palladium. Nickel is plated through an electroless plating process which incorporates phosphorous into the nickel deposit. A thin layer of gold is plated onto the nickel deposit through an immersion process where nickel metal is dissolved and replaced by gold metal. ENIG is susceptible to the issue of hyper-corrosion of the nickel which is known commonly as “black pad”.
ENIG processes have been improved over the years to minimize the risk of “black pad”.
ENIG is one of the more costly surface finishes. ENIG is a flat finish which promotes good solder paste printing. ENIG is also solderable through multiple cycles and has a long shelf life.
Immersion tin is a popular surface finish used mainly in Europe and Asia. The process used to coat circuit boards with immersion tin is as follows. The copper is cleaned and etched to remove contaminates and oxides. The copper surface is prepared for tin plating through a pre-treatment step, then plated with immersion tin. Copper is dissolved into the plating solution as tin metal is plated onto the circuit board pads.
The immersion plating process is self-limiting which limits the maximum thickness of tin. Immersion tin is flat and solders well initially. Lead-free soldering temperatures can damage the finish causing subsequent soldering steps to be challenging. Immersion tin is also susceptible to handling damage because it is relatively thin.
Immersion silver is a finish similar to immersion tin but silver metal is plated over the copper pads. The process used to plate immersion silver onto circuit boards is as follows. The copper is cleaned and etched to remove contaminates and oxides. The copper surface is prepared for silver plating through a pre-treatment step, then plated with immersion silver. Copper is dissolved into the plating solution as silver metal is plated onto the circuit board pads. The immersion plating process is self-limiting which limits the maximum thickness of silver. Anti-tarnish agents are either incorporated into the silver plating step or applied as a final step.
Immersion silver is flat and solders well initially, but can be tarnished through air exposure and by the heat applied for soldering.
Tarnished immersion silver is very difficult to solder. Immersion silver is susceptible to handling damage because it is relatively thin, and must be protected from air and sulfur exposure. Both immersion silver and immersion tin are cost-effective finishes.
With so many surface finishes available on the market, how can performance be optimized for each surface finish? Recently work has been done to test the performance of a variety of solder pastes with each of the surface finishes shown below (Figure 1).
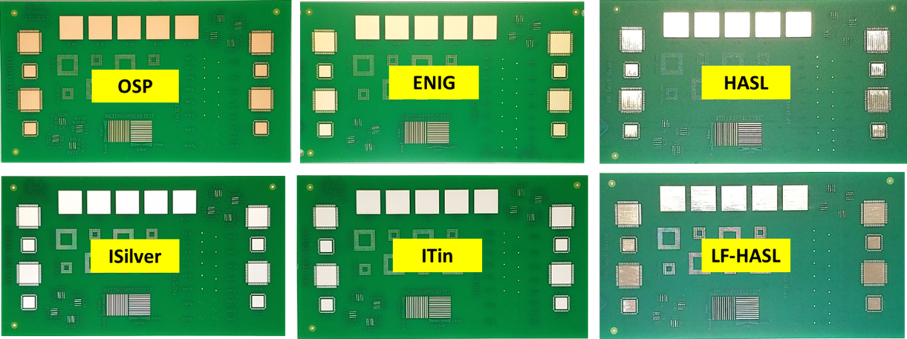
Four different solder pastes were used in this testing.
It includes water-soluble Sn63/Pb37 and SAC305 solder pastes, and no clean Sn63/Pb37 and SAC305 solder pastes. FCT Assembly’s PR test board was used for this evaluation (Figure 2).
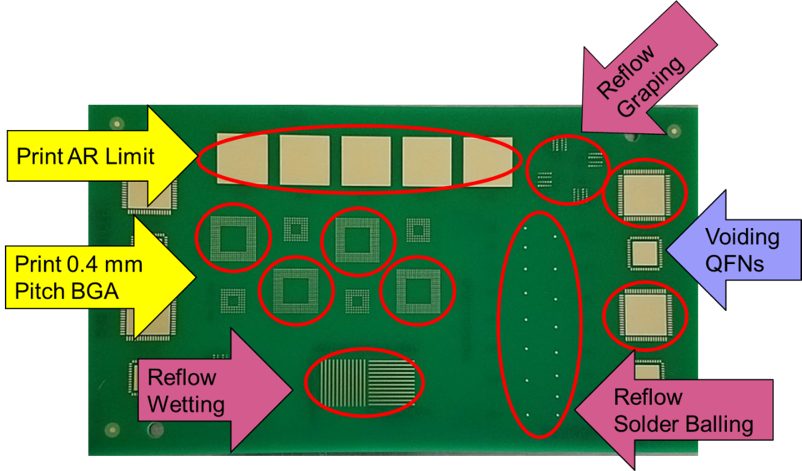
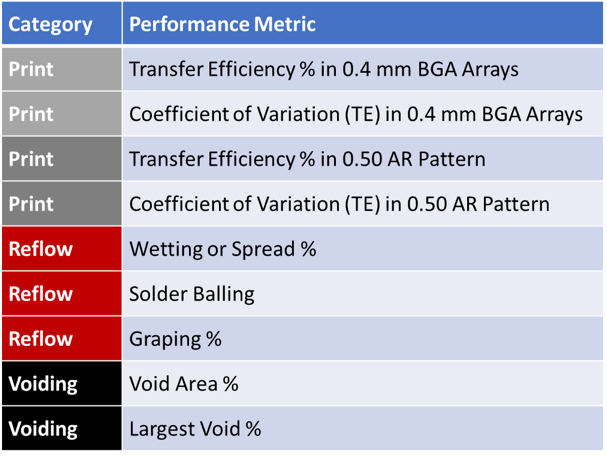
Performance was summarized and recommendations made to help optimize the performance of solder paste with each surface finish. This work will be will be presented at a technical conference.