Solder Paste Flux
Solder paste flux is a gelatinous chemical compound used mainly in combination with solder powder to create solder paste, generally mixed as a 50/50 ratio. Once combined, the paste is a gray, putty-like material.
Solder paste flux serves a threefold purpose:
- Removing any oxidized metal from the surfaces to be soldered
- Sealing out air, preventing further oxidation
- Improving wetting characteristics of liquid solder by facilitating amalgamation.
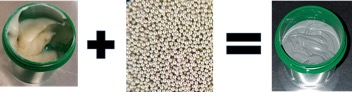
Chemical Properties
Solder paste flux has a very complex chemical composition. It can be comprised of:
- Solvents – liquid used an inert medium to combine the active ingredients, such as water
- Rosins/Resins – high-temperature tolerant, non-volatile chemicals, most commonly forms of glycol
- Surfactants – a detergent used to lower the contact angle of the flux with the surface its applied to, allowing greater coverage
- Activators – chemicals disrupting/dissolving metal oxides, typically acids of various corrosivity
- Rheology Modifiers – any of a variety of compounds that allow a liquid to display Non-Newtonian properties; that is, to change viscosity as pressure is varied
Flux is nearly inert at room temperature but becomes strongly reducing when its temperature is increased. This prevents the formation of metal oxides on both the base and filler materials to which it is applied. It also prevents the beading of the applied solder, facilitating easy flows and application.
Solder paste flux is different than liquid flux in both physical form and activity level. Solder paste flux typically contains 60-80% by weight active ingredients, compared with liquid flux’s 2-25%.
By weight, a mixed solder paste commonly consists of 90% metal. However, the non-metallic ingredients of the flux, due to their lower density, result in their comprising of nearly half the paste volume.
Standards and Definitions
A number of standards exist to define the various flux types. The principal standard is J-STD-004, which categorize fluxes by composition, activity (strength), the presence or lack of halide activators, and reliability from electromigration standpoint and surface insulation resistance (SIR). The J-STD-004 standard for electromigration and surface insulation resistance is >100 MΩ after one week at elevated temperature and humidity with a DC bias applied.
There are three types of solder paste flux:
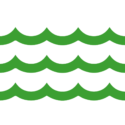
Water-Soluble
Fluxes are composed of glycol bases and organic (carbon-based) materials.
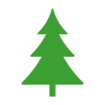
Rosin Based
Fluxes are derived from a pine tree extract.
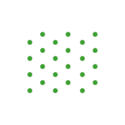
No-Clean
Fluxes are made with resins and various levels of solid residues.
Use
While the main use of solder paste flux is in the creation of solder paste, it is also sold directly as a gel or tacky flux.
Solder paste flux can also act as a temporary adhesive. Its tacky nature holds components together until the heat of the soldering process melts the solder and the parts are fused together.
Once mixed, solder paste is most commonly used in a stencil-printing process. Paste is spread over a stencil in the pattern required on the final end product, a printed circuit board.
The solder paste flux component must have enough tackiness to secure the components while the fixture is processed through the manufacturing line.
Once printed, the circuit board forming process is followed by pre-heating and reflow (melting).
For the flux, the temperature and rate of change in temperature are key in the reflow process. A slow rise in temperature is necessary to prevent solder balling, but must be great enough to activate the flux, then melt the solder itself, and recool quickly enough to retain the desired shape.
Application
Solder paste flux gel can be brushed on where needed and, unlike liquid flux, will not flow away from the application area.
This means that, when used directly as a soldering aid, a small amount of solder paste flux can be used in place of a relatively large amount of liquid flux. Common uses of flux gel include BGA re-balling and the rework/repair of solder joints.
In mixing solder paste flux and solder powder for application to circuit assemblies, there are important considerations:
Working Life
Different types of flux, particularly water-based, can gradually evaporate after mixing, eventually hardening to the point of unusability. Pre-mixed solder pastes have this measurement in time provided by the manufacturer. The working life of self-mixed pastes can be approximated, but should be underestimated for safety.
Viscosity
As a liquid, solder paste is not entirely immune to flow. The thickness of the flux/powder mixture helps determine how well it resists this tendency to hold its shape through the curing process. However, sometimes a lower viscosity is preferred.
When using a squeegee to apply solder paste onto a stencil, the force used to apply can break down the viscosity, which thins the paste and allows it to more easily flow through the stencil apertures. Again, pre-mixed pastes have manufacturer-provided measurements, while custom mixes often require self-testing.
Both working life and viscosity can be expressed through the thixotropic index, a measurement of a mixed solder paste’s viscosity at rest versus applied.
Depending on the ratio and composition of the solder paste flux and solder powder, stirring may be needed at frequent intervals to ensure proper viscosity and test for working life.
The amount of paste is also a key consideration. Too little may cause a joint to lack strength or an electrical connection to have poor conductivity. Too much can result in accidental short-circuits on the board.
Storage & Cleanup
Solder paste flux needs proper storage to maintain usability. An airtight container must be used to prevent evaporation. Storage in an area of a low temperature reduces the rate of oxidation, and thus the rate of degradation of the flux – but take care not to introduce it to freezing temperatures, which can cause separation of the chemicals.
As with all fluxes used in electronics, residues left behind may be harmful to the circuit, and standards exist to measure the safety of the residues left behind.
Each type of flux requires its own solvents for cleanup of excess:
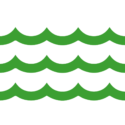
Water-Soluble
Have the widest available range of cleaning agents, generally a mix of deionized water and detergents
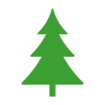
Rosin Based
Require specific chemical solvents, typically involving fluorocarbons.
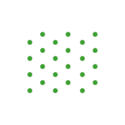
No-Clean
Fluxes, true to their name, generally require little, if any, cleaning.
The residual flux is considered harmless, and can simply be left to dry on the board. Their use necessitates a very clean assembly environment and may need an inert reflow environment.
Washing is still recommended, however, as residual no-clean flux can cause conformal coatings to adhere less effectively.
FCT Assembly manufactures and sells a wide variety of soldering products. These include solder pastes, wire solder, bar solder, liquid flux, and gel flux.
Contact us for more details!